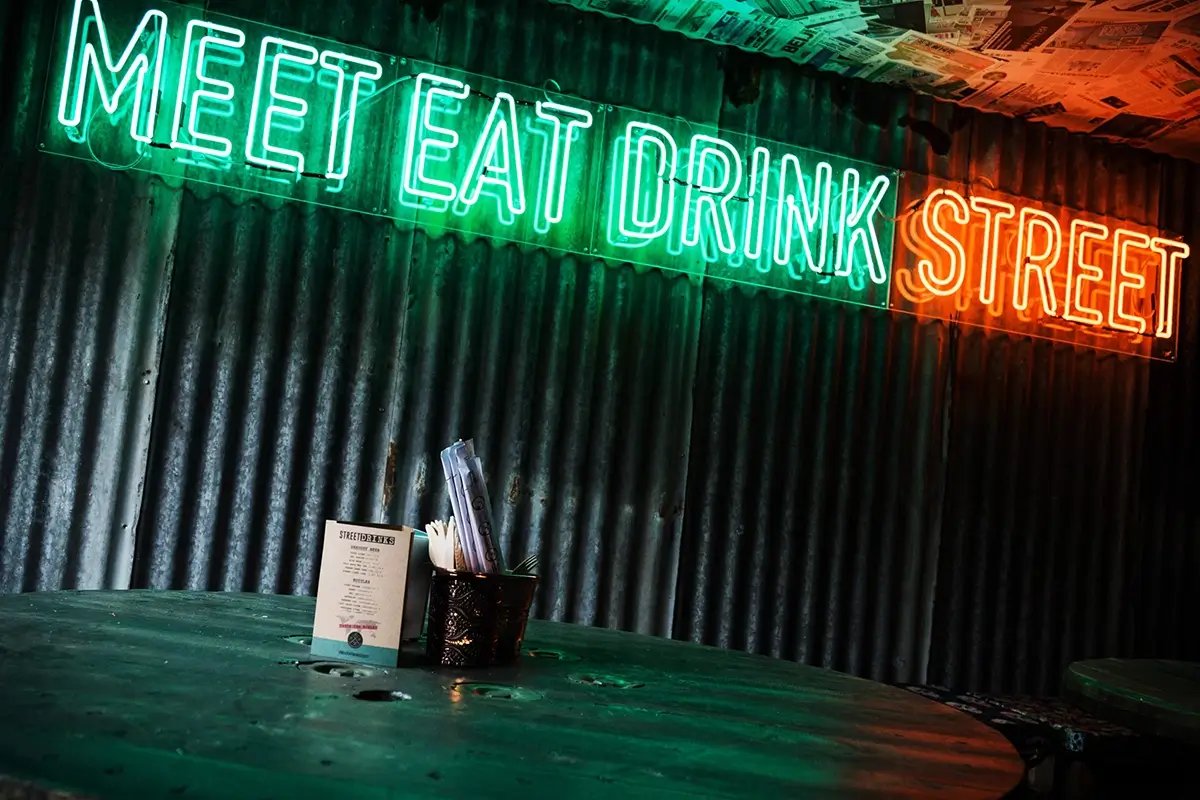
How do Neon Lights Work: A Detailed Explanation
Neon signs are everywhere – illuminating shopfronts, restaurants, hotels, and nightlife districts. Neon signs have been around for over a century, but how exactly do they work? Let’s look at the science behind neon lights, their components, and the process that makes them illuminate.
The Science Behind Neon Lights
Real glass neon signs operate on a principle known as gas-discharge lighting. The process involves an electrical current passing through a sealed glass tube filled with gas, causing the gas to emit light.
This phenomenon is based on the behaviour of atoms when they are energised. When an electric voltage is applied to the neon tube, it excites the gas atoms inside. The atoms absorb energy and then release it in the form of visible light. The specific colour emitted depends on the type of gas used and the coatings applied inside the tube.
Components of a Neon Sign
Neon signs are composed of several essential parts:
- Glass Tubes – The tubes are typically made of soft glass or borosilicate glass, which can be shaped into letters, symbols, or artistic designs.
- Electrodes – Positioned at both ends of the tube, these metal conductors introduce an electric charge into the gas.
- Gas Fill – Neon and Argon gases are commonly used, but other noble gases like krypton and xenon could in theory be used to create different colours.
- Transformers – High-voltage transformers are required to provide the necessary electrical charge to ionise the gas.
- Phosphor Coatings – Most neon tubes have a phosphor coating inside, which reacts with the gas discharge to produce additional colours.
The Neon Sign Manufacturing Process
- Glass Tube Shaping
Neon sign makers, known as glass benders, heat glass tubes over a flame to make them pliable. The softened glass is carefully bent into the desired shape or lettering. The process requires precision and skill to ensure uniform bends and curves, whilst ensuring that the glass doesn’t thin too much on the bends.
- Electrode Attachment
Once the glass tube has been shaped, electrodes are attached to both ends. The electrodes are crucial in conducting electricity through the gas.
- Gas Filling
After the tube is formed, it is evacuated using a vacuum pump to remove all air. Once the tube is completely emptied, a specific noble gas is introduced at low pressure. The choice of gas helps to determine the final colour of the sign.
- Sealing and Electrification
Once the tube is filled with gas, it is sealed, and a high voltage is applied. The electrical current ionises the gas, causing it to emit light. If a phosphor coating is present, it reacts with the ultraviolet light from the gas discharge, resulting in additional colour variations.
- Installation and Mounting
The finished neon tubes are then mounted onto a frame or backing board and connected to a power supply. The wiring is carefully insulated to ensure safety and efficiency.
How Different Gases Create Different Colours
The colour of a neon sign depends on the type of gas used. Here are some common gases and their corresponding colours:
- Neon (Ne) – Produces a classic red-orange glow.
- Argon (Ar) + Mercury (Hg) – Emits a blue or violet light.
- Krypton (Kr) – Generates pale white or greenish hues.
- Xenon (Xe) – Produces a soft blue glow.
- Helium (He) – Emits a pinkish-red colour.
Additionally, phosphor coatings inside the glass tube can enhance or change the perceived colour of the emitted light.
Differences Between Traditional Neon and LED Neon
With advancements in technology, LED neon has emerged as an alternative to traditional neon signs. Here’s how they compare:
Feature | Traditional Neon | LED Neon |
Lighting Principle | Gas discharge | LED diodes |
Power Consumption | Medium | Low |
Durability | Fragile glass tubes | Flexible plastic tubing |
Customisation | Hand-crafted shapes | Moulded or pre-made strips |
Brightness | Warmer, classic glow | Brighter, even illumination |
Lifespan | 8-15 years | 30,000-50,000 hours |
Maintenance | Requires regular checks | Low maintenance |
Traditional neon lights remain popular for their nostalgic glow, while LED neon offers a more energy-efficient and durable alternative.
The Role of Transformers in Neon Lighting
Neon signs require a high voltage to function. This is achieved through step-up transformers that increase the standard electrical voltage (e.g., 120V or 240V) to thousands of volts, enough to ionise the gas inside the tube. The most commonly used transformers include:
- Magnetic Transformers – Traditional and reliable, but bulkier and heavier.
- Electronic Transformers – More compact and energy-efficient, often used in modern installations.
Maintenance and Safety Considerations
To ensure longevity and safe operation, neon signs require proper care and handling. Here are some maintenance tips:
- Regular Cleaning – Dust and dirt can reduce brightness. Clean the tubes using a dry cloth or compressed air.
- Avoid Physical Damage – Neon tubes are delicate and can break easily. Install them in secure locations.
- Check Electrical Connections – Loose wiring or faulty transformers can cause flickering or power issues.
- Ensure Proper Ventilation – Overheating can reduce efficiency, so keep the sign in a well-ventilated area.
- Replace Broken Tubes Promptly – A damaged tube may lead to gas leaks or an incomplete circuit.
Neon signs have a fascinating science behind their operation, from the role of noble gases to the high-voltage electrical processes that bring them to life. While LED alternatives are becoming more common, traditional neon still holds a special place in design and advertising, thanks to its unique glow and artistic appeal.
Understanding how neon signs work not only helps in appreciating their craftsmanship but also ensures better maintenance and longevity. Whether for business, decoration, or artistic expression, neon lights continue to illuminate the world in vibrant and captivating ways.